During my internship in a jewelry studio, I learned the basics of metalsmithing such as wax modeling and casting. To master this craft, I took on experimenting with different forms and methods to achieve distinct shapes.
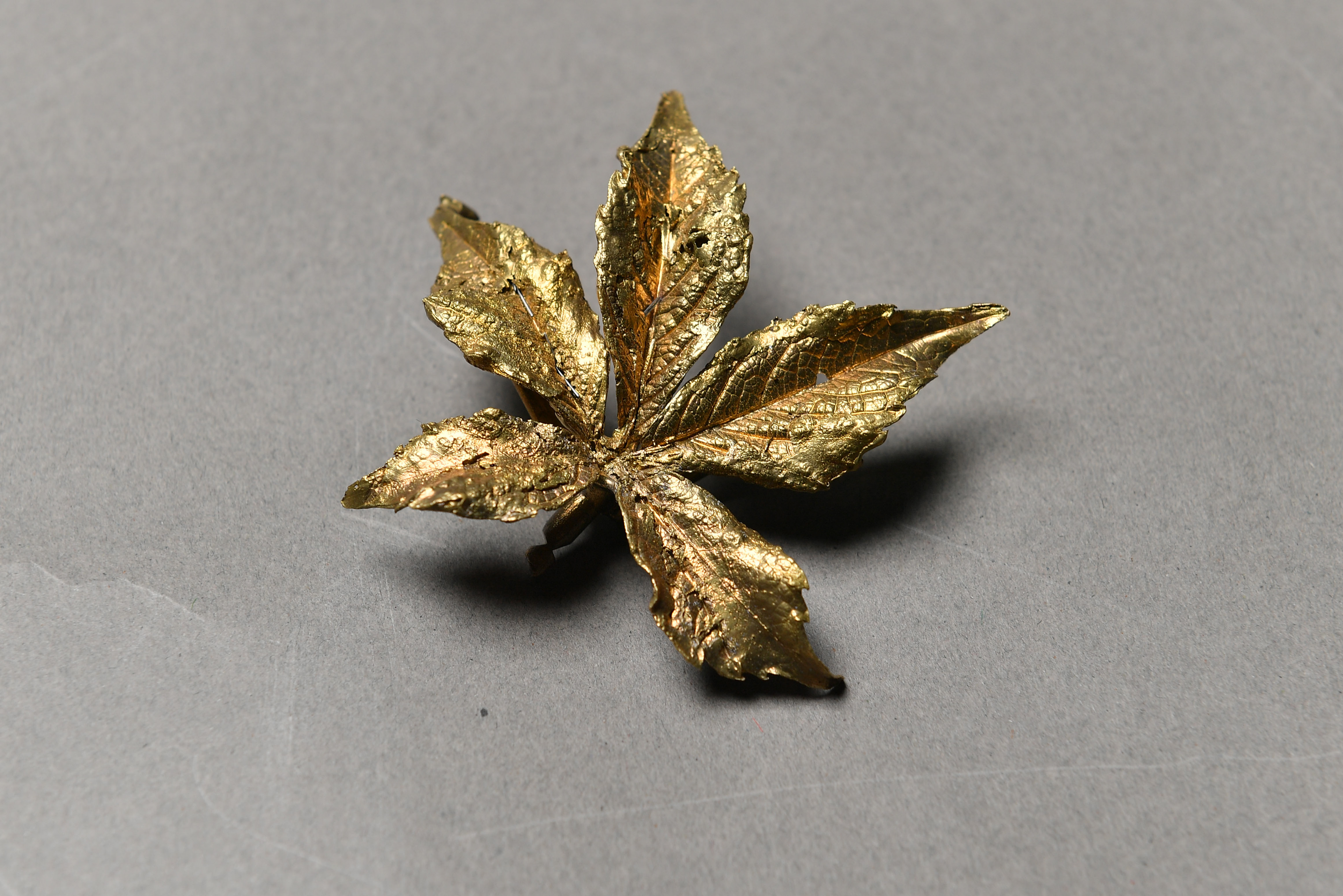
The pendant above was casted from a vine leaf belonging to the Ampelopsis genus. I dried the leaf for several days. The underside of the dry leaf was then coated with wax to ensure that it wouldn't lose its shape during casting. The end product warped a lot, however it kept the leaf shape.
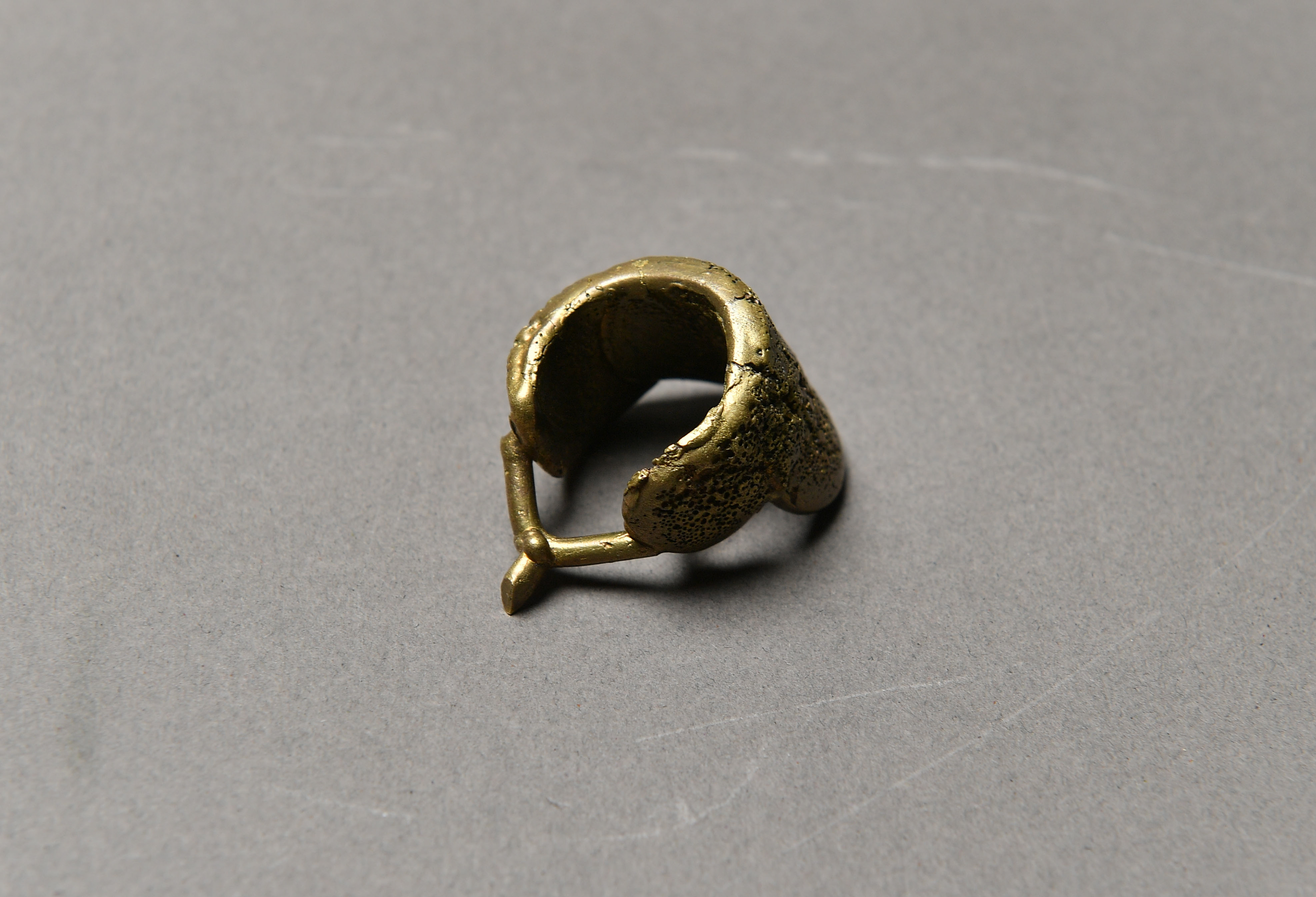
The texture on this model was achieved by pouring molten wax over glass and spraying it with water. Little explosions formed when hot wax came into contact with cold water and resulted in this "granite" texture. I then shaped the textured flat wax around a cylinder to achieve the ring form.
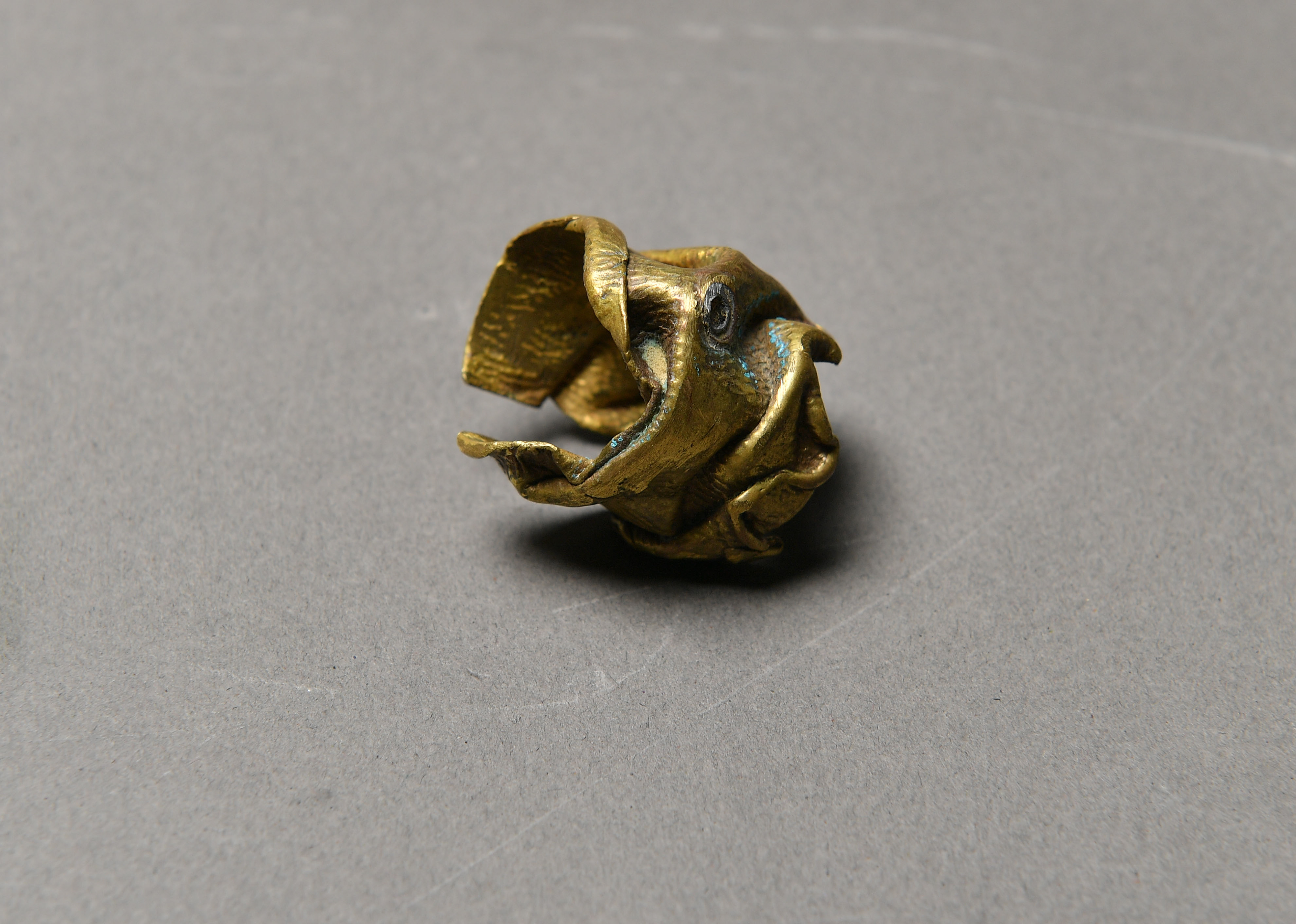
This one was made with very thin wax. As the wax was very thin, I was able to bend it like paper and achieve distinct forms. Also the texture of the ring was produced by etching the wax with a ballpoint pen.
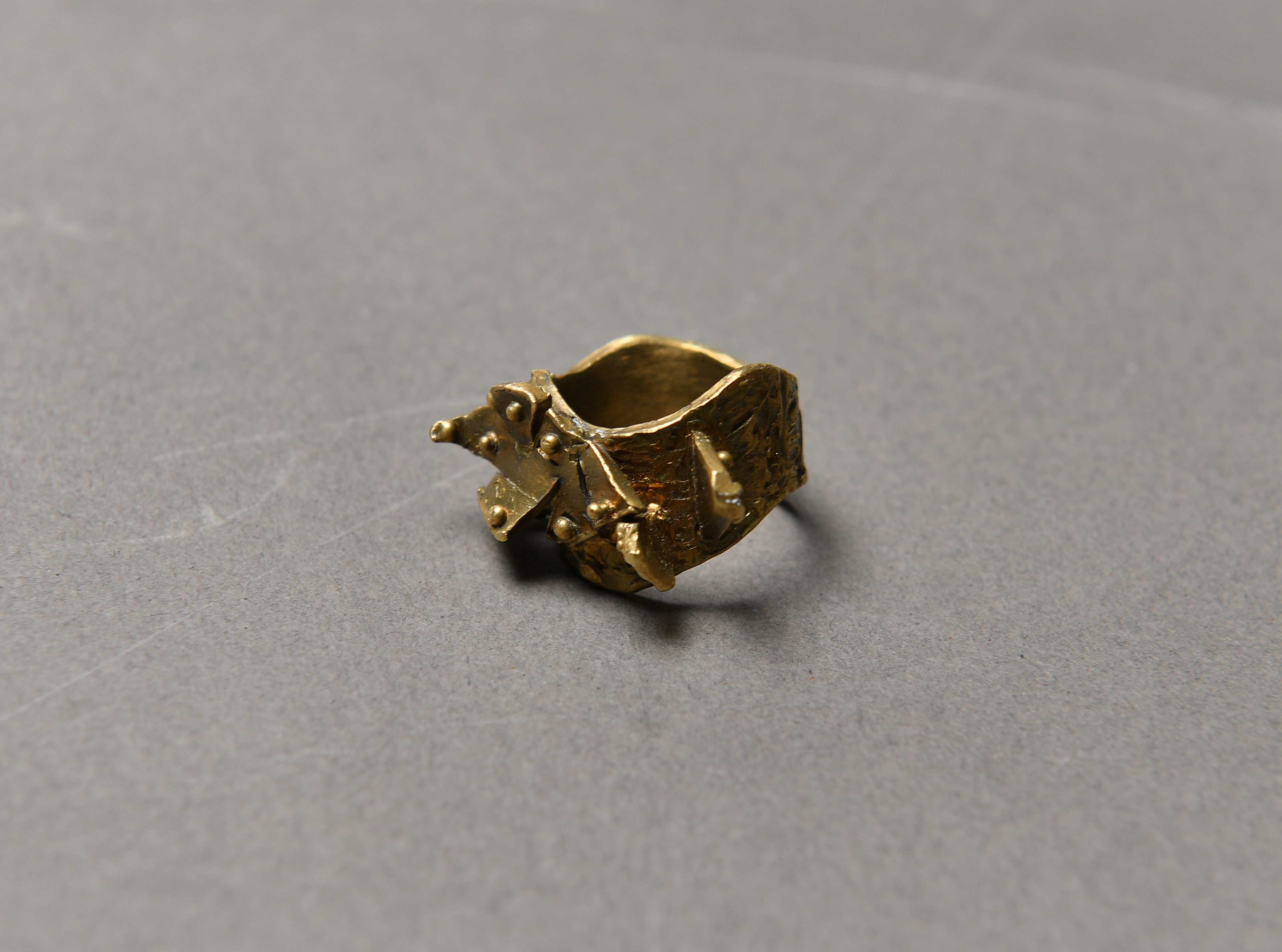
The one above was inspired from contemporary art installations. I thought "installing" sculptures to the ring would add attractiveness to it. I was right to think so.
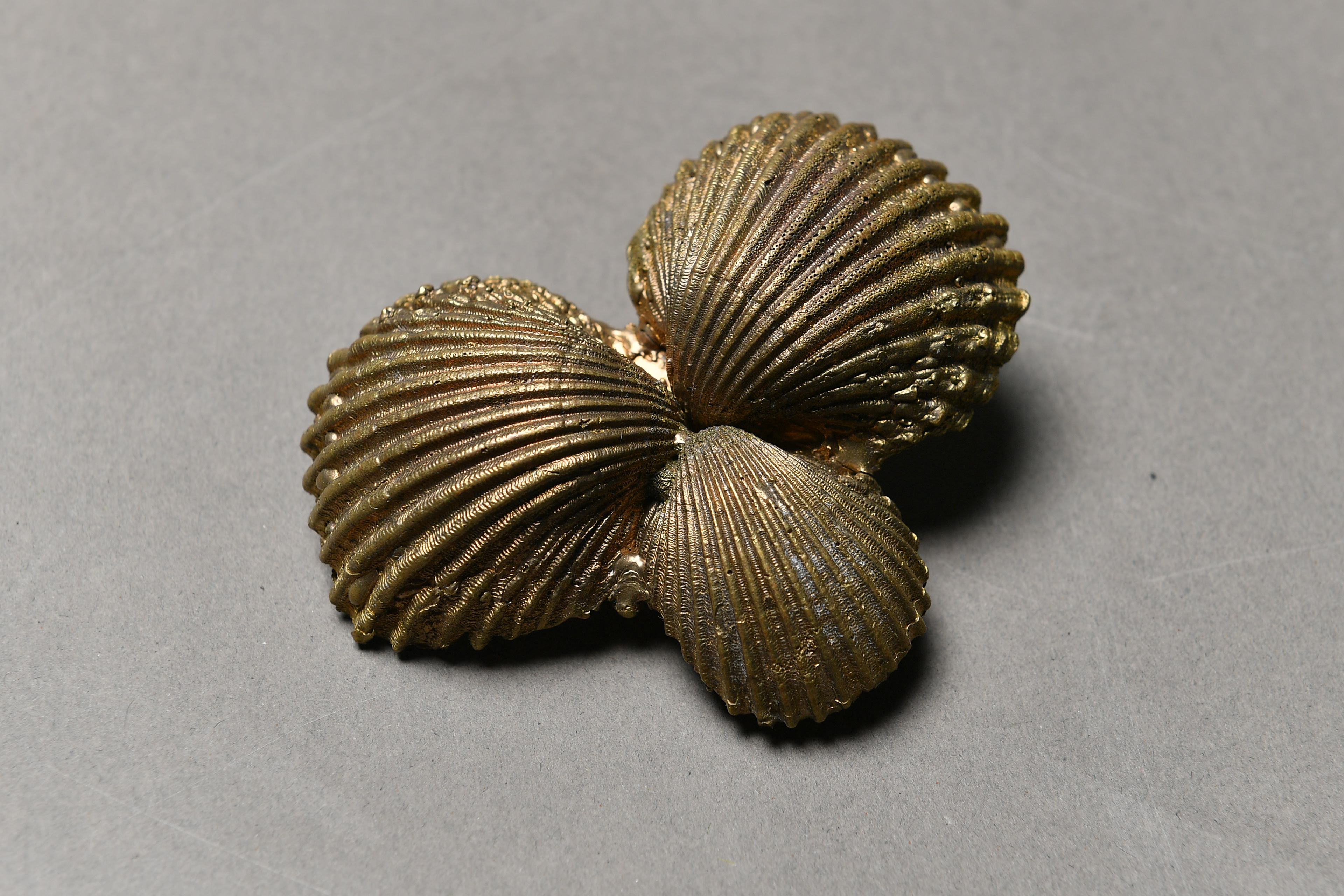
Using silicon construction material, I made molds of several seashells I found. I produced their wax counterparts from these molds. Fusing the wax models, this relatively simple pendant was produced. However, it turned out to be very bulky for comfortable wear. I gave more attention to carving excess wax out in the future designs.
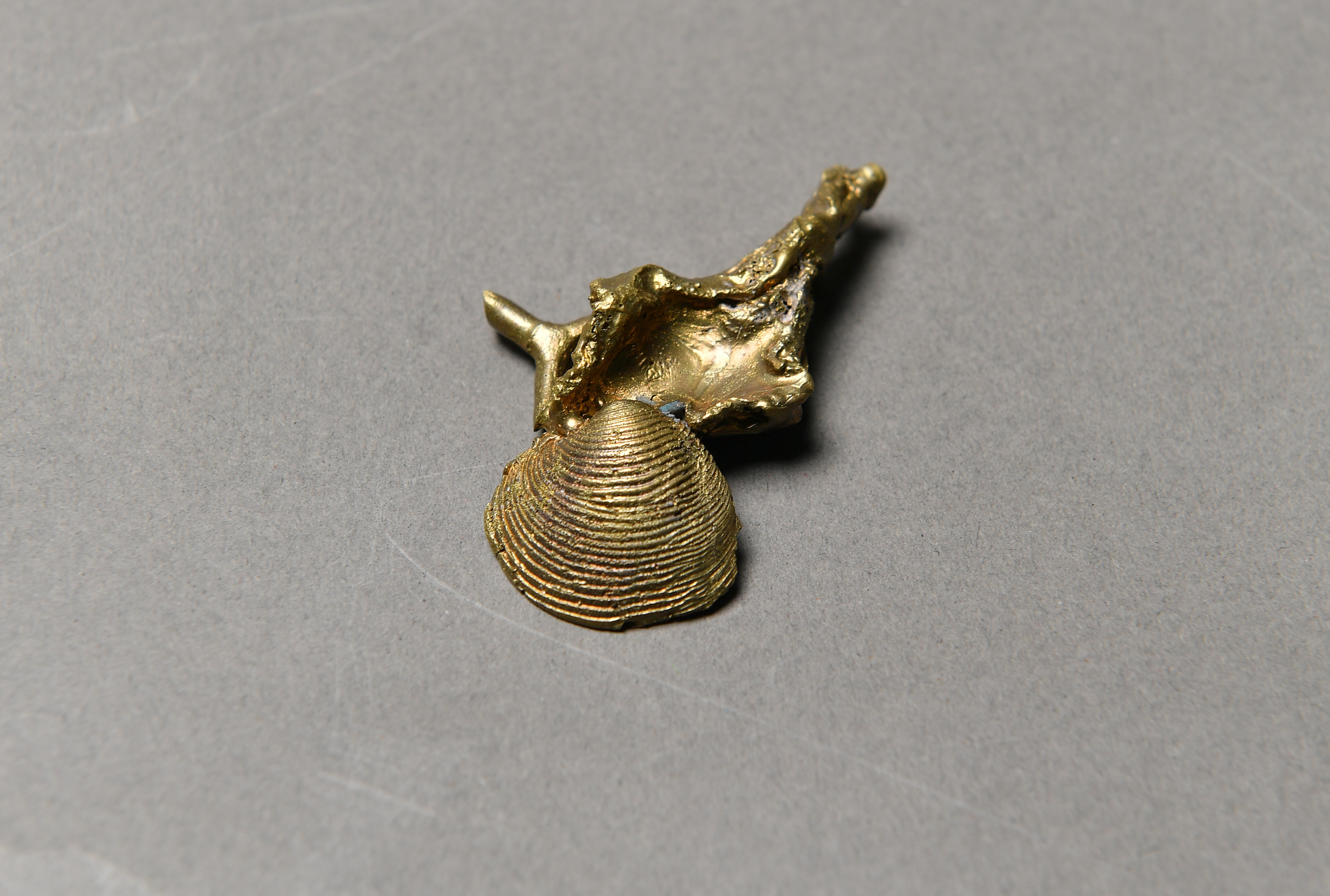
Another seashell model; I made use of napkins this time. By folding napkins to desired shapes and fixing them with wax, I was able to get complex geometric forms. Combining the complex form with the seashell I had this pendant.
All designs were casted with the lost wax method.